A Quality Agreement for Medical Devices
A Quality Agreement for Medical Devices is a formal document that outlines the quality-related responsibilities and expectations between parties involved in the manufacturing, distribution, or supply chain of medical devices. It serves as a contractual agreement between the manufacturer, suppliers, subcontractors, and other relevant parties to ensure compliance with quality standards, regulatory requirements, and agreed-upon quality management practices. The Quality Agreement defines each party’s roles, responsibilities, and commitments related to quality assurance, control, and continuous improvement efforts.
Key Components of a Quality Agreement:
Scope and Purpose: The Quality Agreement begins by defining its scope and purpose, outlining the specific activities, processes, or products covered by the agreement. It clarifies the objectives and goals of the agreement to ensure alignment among all parties involved.
Quality Management System (QMS) Requirements: The agreement specifies the quality management system requirements that each party must adhere to, including relevant standards, regulations, and industry best practices. This may include compliance with ISO 13485, FDA Quality System Regulation (21 CFR Part 820), and other applicable standards.
Roles and Responsibilities: Each party’s roles, responsibilities, and obligations related to quality assurance and control are clearly defined in the agreement. This includes responsibilities for design, manufacturing, testing, documentation, and regulatory compliance.
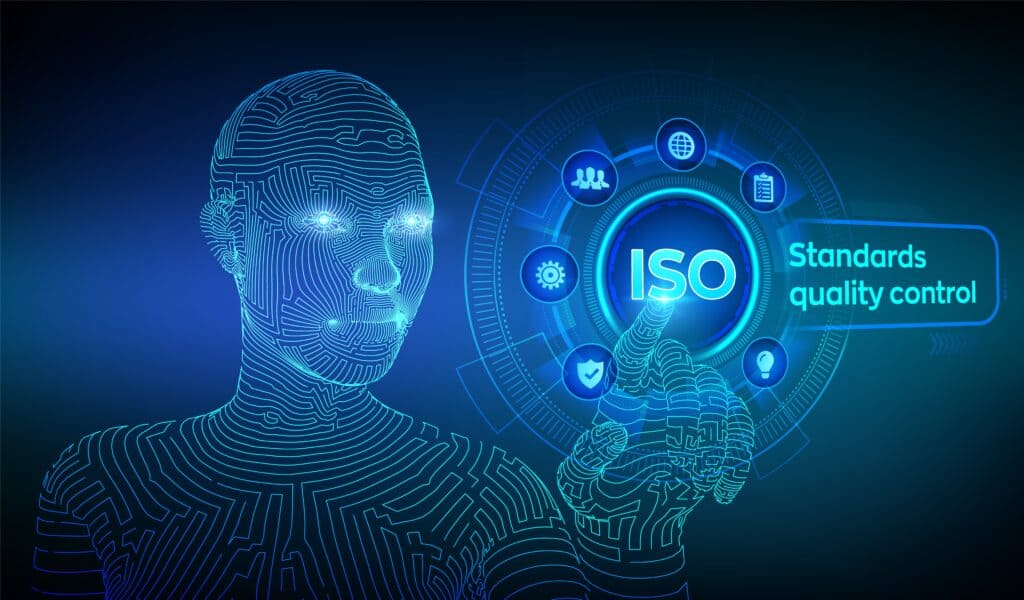
Quality Assurance Activities: The agreement outlines specific quality assurance activities and processes that must be implemented to ensure the quality, safety, and efficacy of the medical devices. This may include supplier qualification, incoming inspection, process validation, and non-conformance management.
Quality Control Measures: Procedures for quality control, monitoring, and testing of materials, components, and finished products are detailed in the agreement. This ensures that quality standards are consistently met throughout the manufacturing and supply chain processes.
Change Control Procedures: The agreement establishes procedures for managing changes to processes, materials, specifications, or other aspects that may impact product quality. Change control processes ensure that any changes are properly evaluated, documented, and communicated to all relevant parties.
Audits and Inspections: The agreement may include provisions for conducting audits, inspections, or assessments to verify compliance with quality requirements. This may involve on-site audits, supplier audits, or third-party inspections as necessary.
Communication and Reporting: The agreement defines communication channels and reporting mechanisms for sharing quality-related information, such as quality metrics, performance indicators, and adverse events reporting.
Relevant Standards and Regulations:
ISO 13485: Medical Devices – Quality Management Systems: ISO 13485 sets out the requirements for a quality management system specific to the medical device industry. Compliance with ISO 13485 is often a prerequisite for market access in many countries.
FDA Quality System Regulation (21 CFR Part 820): The FDA’s Quality System Regulation establishes requirements for the design, manufacture, and distribution of medical devices sold in the United States.
EU Medical Device Regulation (EU MDR): The EU MDR sets forth stringent requirements for medical device manufacturers, including the need for quality agreements with suppliers and subcontractors.
ICH Q10: Pharmaceutical Quality System: While primarily focused on the pharmaceutical industry, the principles outlined in ICH Q10 for establishing and maintaining a quality management system are applicable to medical device manufacturers as well.
By establishing a Quality Agreement, parties involved in the manufacturing and distribution of medical devices can ensure consistency, compliance, and accountability throughout the supply chain. This helps mitigate risks, enhance product quality, and maintain regulatory compliance, ultimately contributing to the safety and effectiveness of medical devices for patients.